Tack & Farm
Our Tack & Farm section features an Apparel section to find both practical and fashionable riding attire. If you ride English & Western or Race, many sources are available in the Tack section.
Building a barn? Need an architect for your equine dream home? Find one in Barns & Stalls.
Have a hungry horse? Of course you do! Find a place to buy your feed and tuck your horse in at night in the Bedding & Feed section. Looking for a place to keep your horse? You can find it in the Horse Boarding section. Keep your horse happy and beautiful with resources in our Grooming section.
Traveling? Find a Shipping company or Horse Sitting service if your horse is staying home!
Running and maintaining a farm or stable is a continuous effort, and to help find products or tools you need, please see our Equipment, Fencing and Management Tools sections.
Seeking Services? Find financial and tax expertise in our Accounting section. Companies who will help protect your investment are found in the Insurance section. For those who want legal advice about purchasing, liability, and other issues, please look at the Equine Law section to find an expert. Build and promote your business with teams from Marketing / Videography / Web Design.
Do we need to add more? Please use the useful feedback link and let us know!
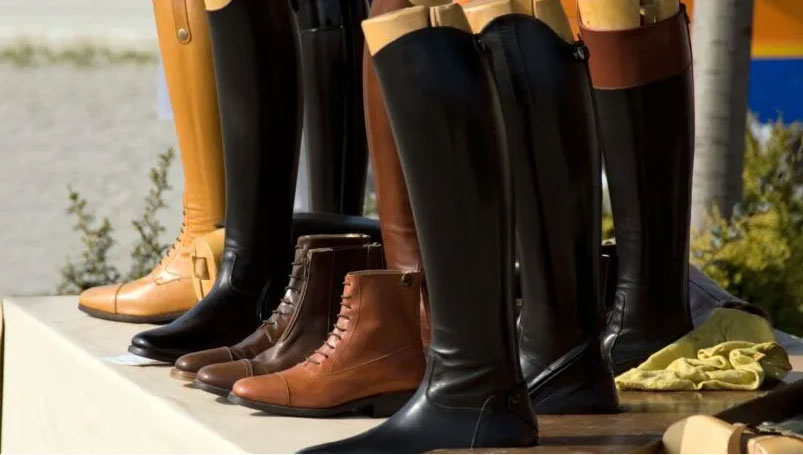
by Natalie Gasper
The Great Boot Height Dilemma If you’re anything like me, you’re always checking out other riders’ footwear in the barn aisle. After all, boots are a key component of a good ride, which means it’s important to choose the best pair. But how do you choose between a short boot and a tall boot?
Riding boots come in a range of heights, from short boots to tall boots. Short boots are generally ankle height and tall boots usually go to the knee. For Western riders, there’s a convenient mid-boot option that comes to about mid-calf. Many riders will wear different boots for practice than for show.
While both short and tall boots are appropriate for riding, many riders prefer the stability and protection of a tall boot.
Boot height definitions vary somewhat between English and Western riding disciplines. In general, a short boot is no taller than mid-calf, more commonly ankle height. Tall boots are mid-calf and taller (though they often hit just below the knee).
When to Wear What
English riding boots are most broadly separated into short boots (paddock and some muck boots) and tall boots.
Practice
When schooling, many riders may opt for a paddock boot and a pair of half chaps. More advanced riders may school in a leisure pair of tall boots. And some riders will hop on in a pair of muck boots (make sure they have a one-inch heel!).
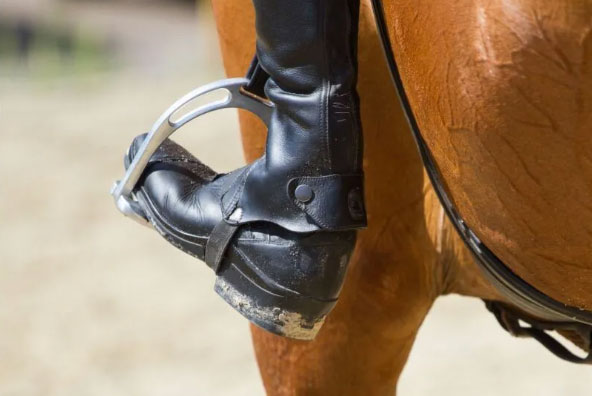
Show
Shows almost always require a tall boot. At some of the lower levels, paddock boots with half chaps are acceptable.
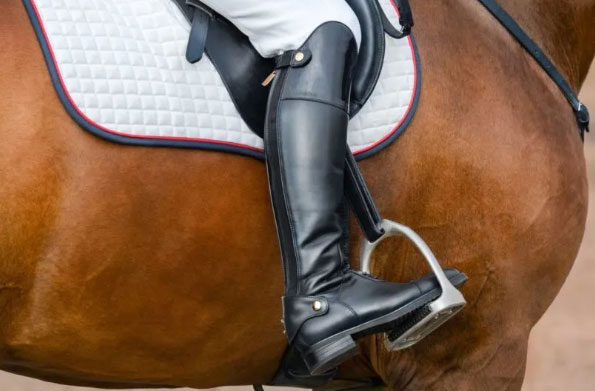
Various Styles of English Boots
- Paddock boots (short)
- Tall boots (show)
- Tall boots (leisure)
- Muck boots (short or tall depending on type and season)
Tall & Short Western Riding Boots
Western boots have a wider range of heights, so it can be more challenging to find the right height. A pair that works great for chores may not be the right height for riding.
There are three main western boot heights.Short (6” – 9” uppers)
Pros: Short boots, like Ropers, are a more recent design that also tends to have a lower heel. They are very comfortable for doing barn chores and the designs tend to feature flexible soles for improved fit.
Cons: The tops have a habit of getting stuck on the saddle’s fender, which can be annoying.
Mid (9” – 11” uppers)
Pros: Mid-height boots offer the best of both worlds, being equally suited for working and riding. The heels tend to be a bit lower than other styles, which makes being on your feet all day a breeze. Plus, the soles usually have treads and cushioning (anti-slip + comfort for the win).
Cons : These boots tend to be more affordable than other options, which means they can have a cheaper look. They’re also not as intricate in their designs as other boots.
Tall (12”+ uppers)
Pros: These boots are similar in many ways to mid-height boots. The heels tend to be higher, and riders often love the ankle and calf support & protection of these boots. Plus, at a higher price range, the designs tend to be stunning and the leather of great quality.
Cons: Depending on the exact height, tall boots may be too tall for showing (the taller the boot, the bulkier they tend to look under pants). Many of the taller boots (13”+) may be better suited as fashion boots than functional riding boots.
Frequently Asked Questions
Q: Are tall boots better for riding?
If you’re an active competitor in eventing, dressage, hunters, or jumpers, tall boots are worth the investment. Otherwise, a short boot (like a paddock boot) works just fine.
Q: How tall should riding boots be?
This really comes down to personal preference. For English riders, some love them tall and others prefer a shorter boot. For Western riders, you’ll want a slightly taller boot (10+ inches) to avoid stirrup and saddle issues.
Q: What are the benefits of tall boots?
Tall boots can prevent pinching or chaffing from the stirrup leathers, while providing extra protection (and extra warmth in the winter). Some riders feel tall boots keep their legs more stable.
Q: When should I get tall boots for riding?
Tall boots are expensive, so wait to invest in a pair until you’re moving up the levels or in a consistent show program.
Parting Thoughts
This age-old debate will likely never be settled, so don’t be afraid to experiment with boot height to figure out what works best for you.
This article originally appeared on Horse Rookie and is published here with permission.
You can read more interesting articles in our section on Tack & Farm.
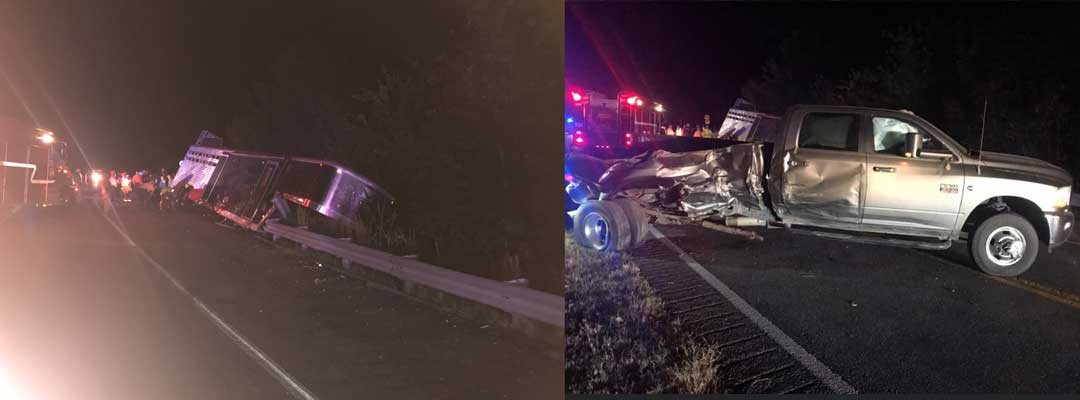
5 tips for safe horse hauling, including the invaluable importance of horse shipping boots
Kailey Schmidt was at the wheel of a truck pulling three horses home from a college rodeo. Two friends, also members of the University of Tennessee-Martin rodeo team, were with her in the cab. It was 11 o’clock at night when Kailey noticed a car was speeding toward an upcoming intersection. The driver didn’t see the stop sign he was soon to blow past. Kailey did and pulling a 42-foot trailer with horses, she knew there wasn’t time for them to stop. She stepped on the gas with hopes of making it across the intersection.
The oncoming car T-boned the bed of her truck, sending their truck spinning so fast that it slammed against the living quarter compartment of the horse trailer, detaching completely from the gooseneck hitch. The horse trailer’s emergency brake cable allowed it to come to a standstill; however, its resting place left the horse compartment dangling on top of guardrails over a 30-foot drop to a gully.
“If that car would have been a few seconds earlier, it would have killed all three girls -- and just a few seconds later, killed all three horses,” said John Luthi, head coach of the UTM rodeo team.
As the three women stepped from the truck, they were each unharmed but in shock. “I looked up to see our horse trailer on the edge of rolling off a gully,” recalled Kailey Schmidt. “When I picked up my phone to dial 911, I couldn’t believe the words coming out of my mouth.”
The horses and trailer were teetering on the guardrails, and it wasn’t safe to get on to help the horses. “It would be silent, and then the horses would start thrashing really bad. I could hear the horses struggling to get up. We were able to cut their lead ropes so they wouldn’t choke,” Schmidt said.
One of the horses on the trailer was Tater, who was gifted by Kailey’s parents for her 13th birthday.
Getting the Horses Out Safely
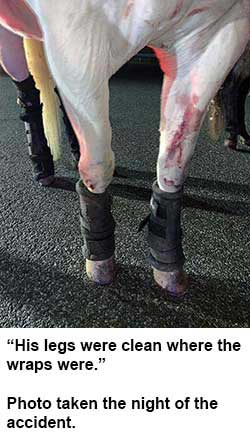
Half of the UTM rodeo team was miles behind them, and soon 10 horse trailers were parked on the side of the highway. They were there for emotional support and to lend a hand however they could. Sometime later, a wrecker arrived to remove the horse trailer from atop the guard rails to safety.
“One horse was trailered immediately to an emergency vet clinic. He was left with severe injuries and a long road to recovery,” recalled Schmidt.
“My horse was the only one who could pull himself up on his own. He was the only one wearing Back on Track wraps that night. The wraps played a huge part in enabling him to recover so fast. Admittedly, a lot of the time you’re just ready to hit the road but thankfully that night, I put on his Back on Track wraps before I left the rodeo. With the wraps, he was thankfully not cut up down his lower leg or severely injured. His legs were clean where the wraps were. To this day, he is the only horse on that trailer that is back riding or competing after the wreck. Just four short weeks after the wreck, he was back to competing at Southern Arkansas University, and we won third in the long round tying goats.”
5 Safety Tips For Hauling Your Horse
- To help prevent injury while transporting your horse, wrap your horse’s legs or secure horse shipping boots or therapy boots.
- Always pack an equine first aid kit, even if you’re only traveling a few miles down the road.
- Ensure your vehicle is rated for the tow capacity to pull your horses and trailer.
- Make sure you have the right size of trailer ball for a secure fit to avoid a trailer coming unhitched.
- Always double-check that your tires are fully aired without cracks, all doors and slants are secure, trailer lights work properly and the hitch is completely secure before transport. See our selection of trailering supplies.
Healing After an Accident
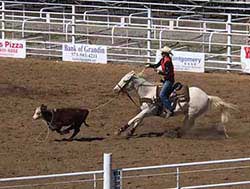
Kailey’s love for horses started as a young girl, and like many, she has never grown out of it. “I was born and raised in the horse world. When I was a toddler, I wouldn’t go to sleep unless they walked me down the barn hallway every night.”
She knows she is lucky to still have her 13th birthday present Tater with her today, and that they can continue their riding and love for rodeo together. “He was the first colt I ever broke, and I was pretty green myself. We have learned together.” A finance major, she has two more years with UTM competing in “Everything they let me,” she said, which includes: goat tying, breakaway roping, team roping and barrel racing.
When asked how she has overcome such a traumatic accident, Kailey paused. A few moments later she continued, “You have flashbacks, but you have to accept it and move on. You can’t live life in fear. Keep moving forward.”
She credits UTM rodeo team head coach John Luthi for his inspiration and her positive perspective. Luthi has been a well-respected name in the rodeo ranks since he was a contestant, as five-time Prairie Circuit qualifier in bareback riding and a three-time qualifier in bull riding. He won 15 all-around saddles during his 22-year career as a contestant. As a college rodeo coach for now 39 years, his passion for the sport, and mentoring his team, is unwavering.
“Our rodeo team is on the road a lot,” said Luthi. “You have to have faith that you’ll make it and that things will be fine. We do a lot of praying and that’s part of life. It’s like when you get out of bed in the morning, you step off, and you have faith there’s a floor beneath your feet. You have to have faith and trust that things are going to be fine.”
This article originally appeared on Valley Vet and is published here with permission. Valley Vet Supply was founded in 1985 by veterinarians for people just like you - people who want the very best for their four-legged friends and livestock.
All photos courtesy of Valley Vet.
There are more informative articles in our section on Tack & Farm.
Chuck is back with another episode of the Leather Element! In this video, he goes over a few rare tools you may want to invest in for your shop. Although these tools aren't used as often as our knives and chisels, they're still good to have on hand in case we need them.
Read more: The Leather Element: Rare Tools - Weaver Leathers (8:53)
Daniel Reach is here to answer your questions and share some tips and tricks for keeping your basketweave stamps perfectly straight on any project. With just a few prep steps, like setting a base line and angle line, you'll achieve a neat, precise basketweave in no time! We hope these tips help, and if you have more questions for Daniel, drop them in the comments!
Read more: Keeping a Straight Basketweave Stamp Design - Weaver Leathers (4:27)
- Cornell Equine Seminar - Mud Management on Horse Farms (59:59)
- Two-point, Half-Seat and Light Seat explained with Teresa Kackert (7:05)
- Back in the Saddle
- Breast Collar and Back Cinch Adjustment with Julie Goodnight (6:46)
- Howard Council: A Humble Legend
- How is a Saddle Custom Made for the Rider (5:21) - Saddlefit 4 Life
- The Extraordinary Talent of Bill Knight
- The Extraordinary Talent of Bill Knight (2)
- Saddle Fit for Women's Anatomy (2:47) - Saddlefit 4 Life
- Davis Reynolds: Full-Service Saddlemaker